FORCITIS wins first prize in China Resources Land's ultra-low energy consumption project curtain wall connection scheme competition
Recently, FORCITIS won the first prize in the "ultra-low energy consumption project curtain wall embedded parts and adapter connection scheme competition" jointly organized by the Engineering Management Department and Design Management Department of China Resources Land Shanghai Company, thanks to its outstanding design concept and technical strength.
This honor is not only a recognition of FORCITIS' technological capabilities, but also a high affirmation of its innovative solutions in the field of ultra-low energy buildings.
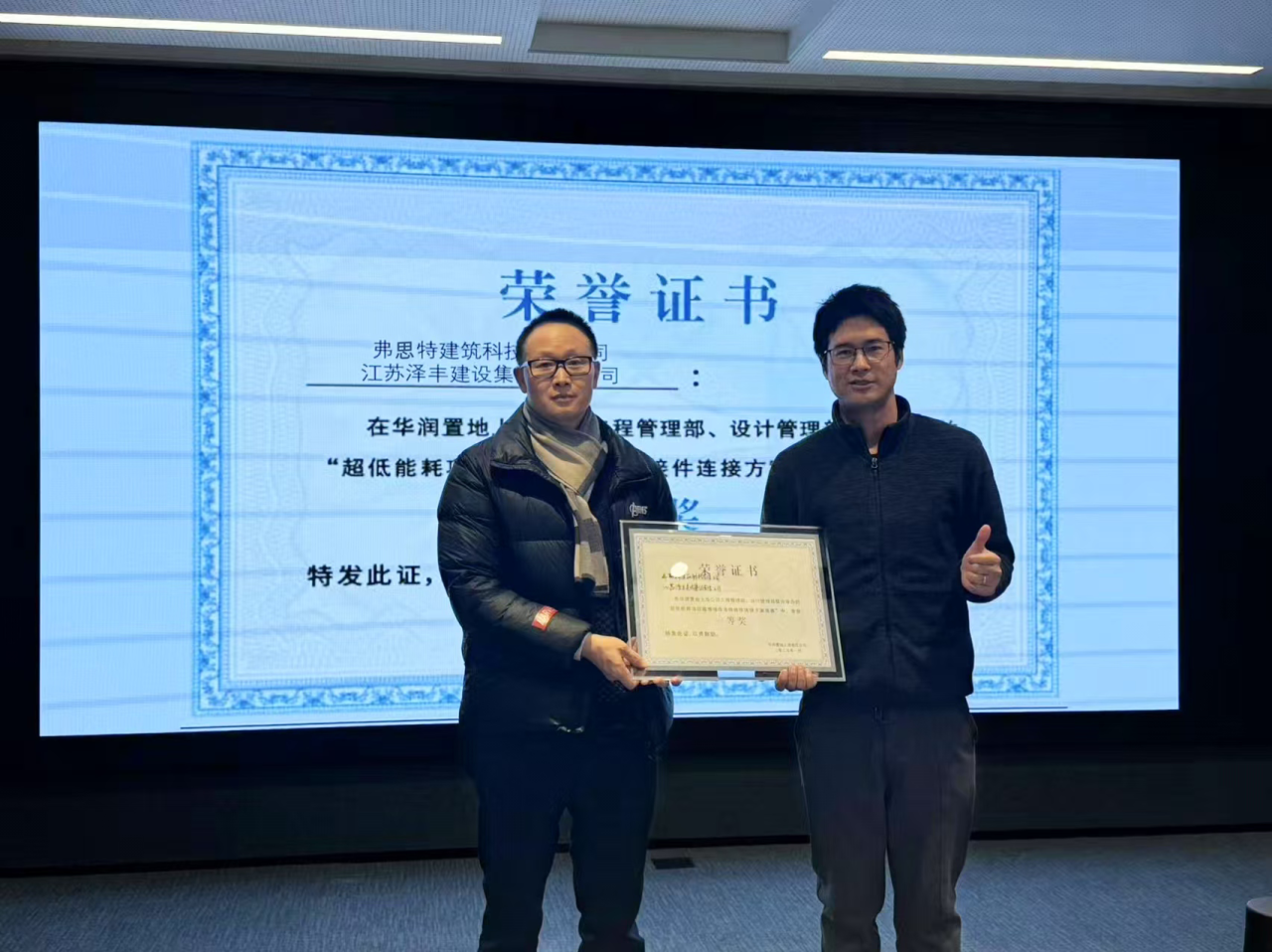

Background and Topics of the Event

With the increasingly strict requirements for ultra-low energy consumption and near zero energy consumption buildings in Shanghai, many projects are facing huge challenges in terms of embedded parts process and quality, while cost control has also become a major challenge.
To address these challenges, China Resources Land has convened multiple consulting and construction units to jointly discuss and find more optimized methods for embedded parts, in order to promote the sustainable development of the construction industry.
Technical Seminar and Cooperation
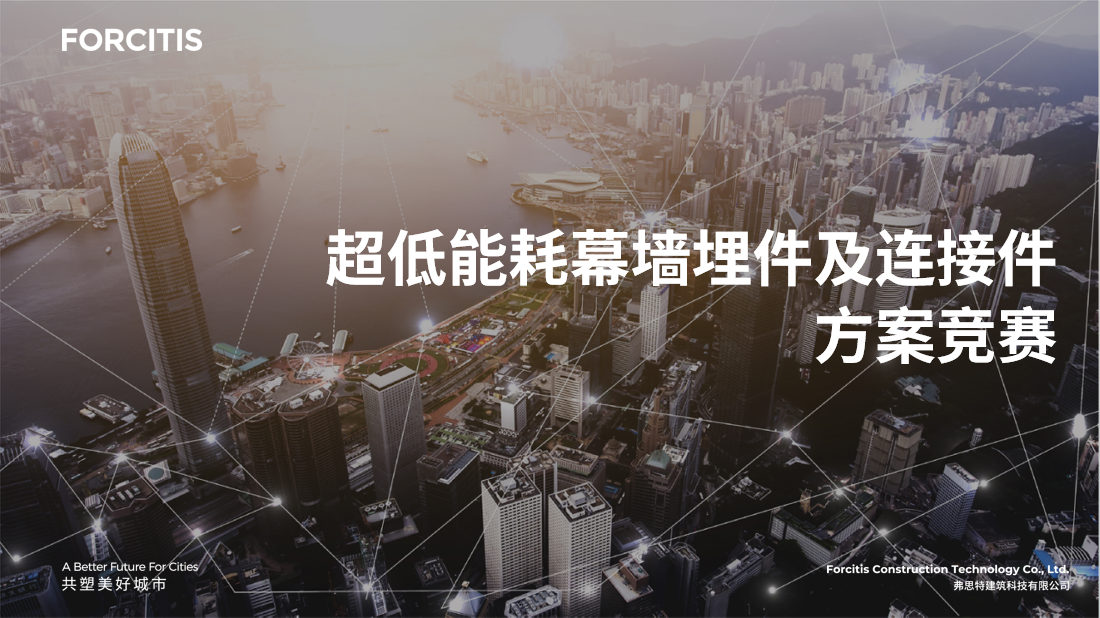

In this competition, FORCITIS actively engaged in in-depth exchanges with experts from various fields, sharing its rich experience and latest research results in the field of green building, and jointly exploring optimization solutions with multiple consulting and construction units.
Through detailed on-site research and technical analysis, ensure that the proposed solution not only meets regulatory requirements, but also effectively improves construction efficiency and reduces costs.
FORCITIS' Solution
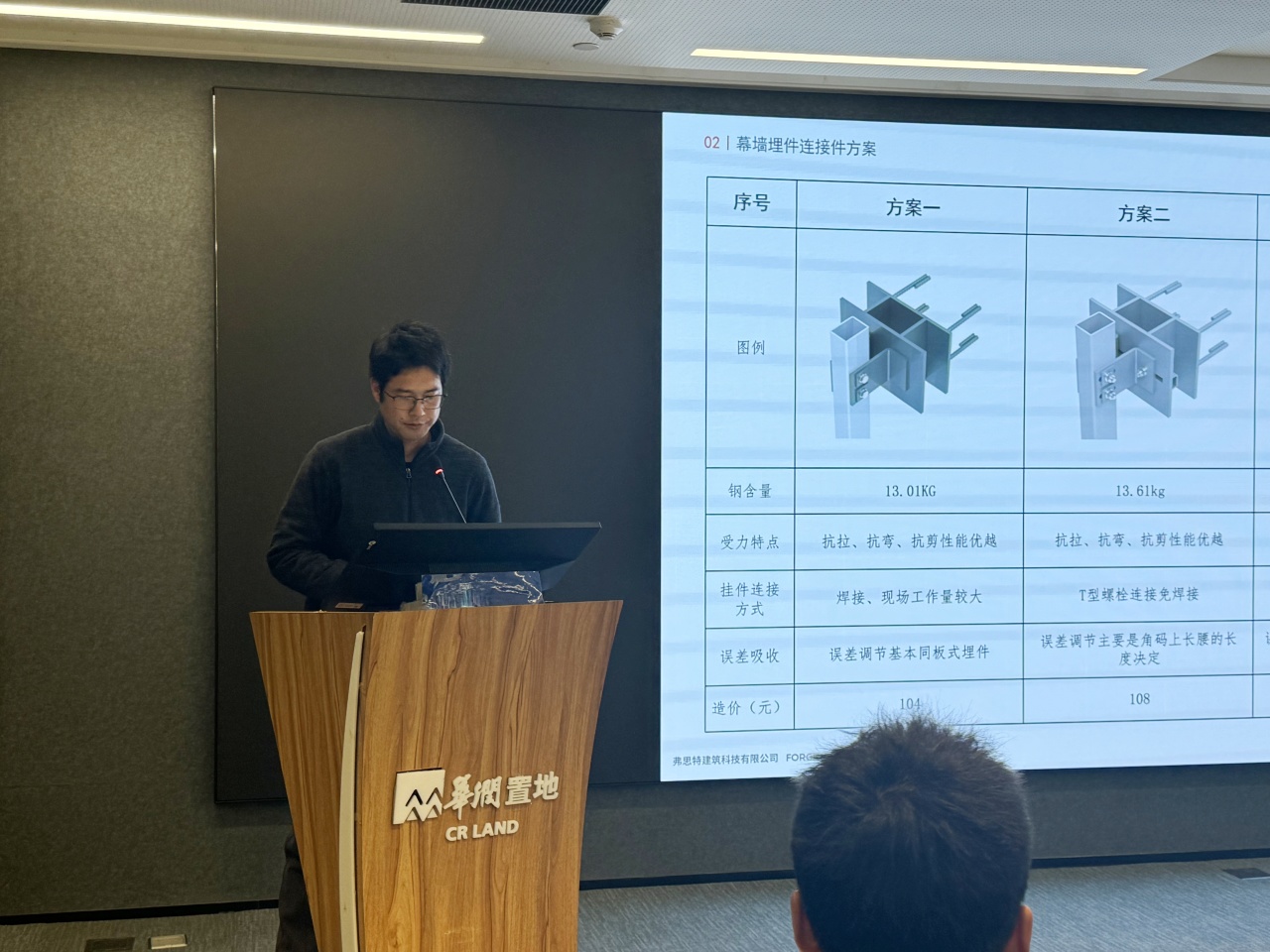

The following are the core technological highlights showcased by FORCITIS in the competition:
Adopting a welded adjustment design, the rear structure is consistent with conventional flat embedded parts, and the front end is extended by welding vertically reinforced steel plates to form a high stability support.
Its column corner code is directly welded to the embedded steel plate, with outstanding tensile, bending, and shear performance, especially suitable for high load scenarios.
Large range error adjustment can be achieved through welding technology, but on-site welding operations are required, the construction period is long, and local cutting of the cavity insulation layer is needed.
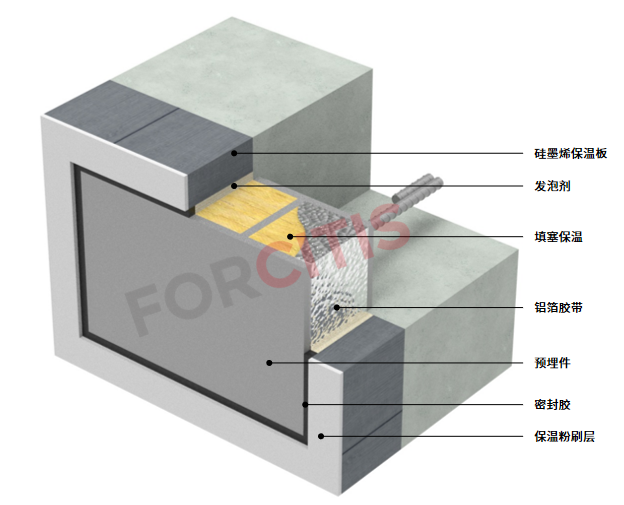

This scheme is a welding free bolt adjustment type, designed with T-shaped bolt slots and long bolt holes at the front end, combined with a rear stiffening plate avoidance structure to achieve non welding connections.
The corner code of the column is fastened by T-bolts, and the installation process does not require hot work, with high construction safety and strong horizontal adjustment ability. Its stress performance is equivalent to scheme one, but the insulation layer still needs to be cut, which is suitable for conventional curtain wall engineering.
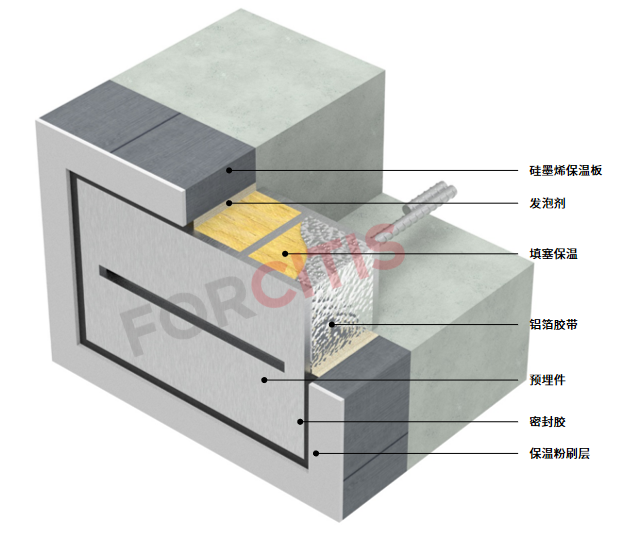

This scheme is based on the design of a π - shaped aluminum alloy pendant, utilizing the long waist hole of the pendant base to achieve multi-directional mechanical adjustment, and the error absorption ability depends on the structure of the pendant itself.
The full bolt connection method further simplifies the installation process, and the aluminum alloy material reduces its own weight, making it suitable for scenarios with high precision requirements. But the adjustment range is slightly smaller than the welding scheme, and the error tolerance needs to be planned in advance. The insulation cutting requirements are consistent with the above scheme.
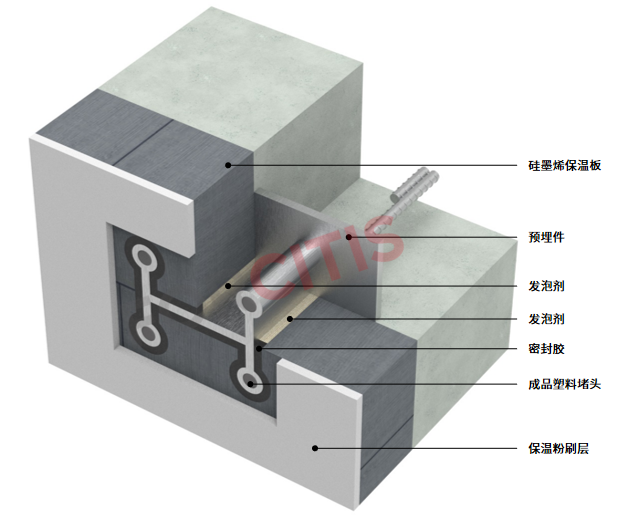

This scheme adopts customized embedded parts, using steel plates as anchor bars embedded in concrete, and the front end is designed as groove type embedded parts to reduce on-site welding workload.
Although components have been added to the front slot to enhance certain performance of the pendant, overall, its tensile, bending, and shear properties are slightly inferior to traditional flat embedded parts. Therefore, for cantilevered components such as canopies, especially those that require resistance to large bending moment reaction points, this scheme is not the best choice.
The advantage of this solution is that it reduces the need for on-site welding and provides good three-dimensional adjustment capability. In addition, it reduces the workload of insulation layer treatment and is suitable for standardized rapid engineering.
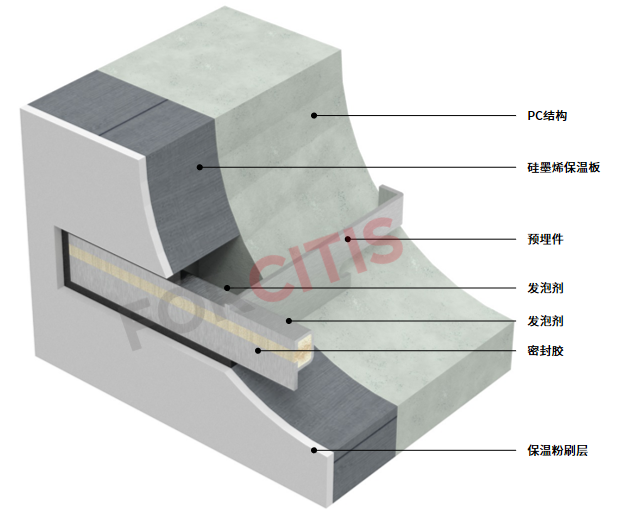

In summary, each of these four solutions has its own focus and solves key issues in ultra-low energy curtain wall systems from different perspectives, including but not limited to structural stability, insulation performance, and construction convenience.
Adopting a "zigzag" bent steel plate component, insulation material is filled in the cavity during pre embedding, and the gap between the insulation layer and the embedded part is treated with foaming agent and sealant. It is suitable for nodes that require complex cavity insulation.
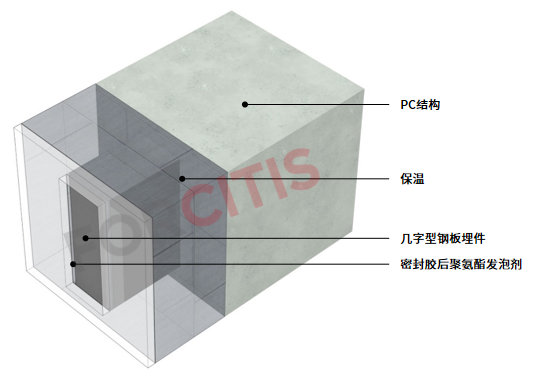

Adopting a "Z-shaped" single bent steel plate, the structure is simpler, mainly relying on foaming agent to fill the gap between the steel plate and the silicone insulation layer, and sealing the gap with outer sealant. The construction process is simpler, suitable for scenarios with higher efficiency and cost requirements.
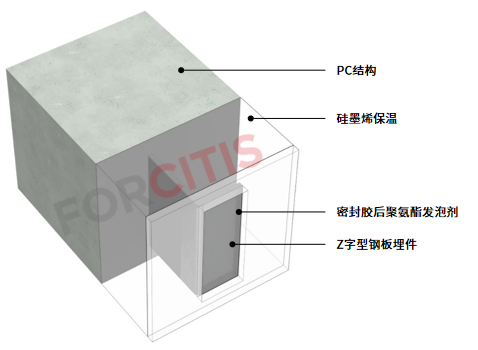

In summary, the core differences between the two schemes lie in the shape of the steel plate, the insulation treatment method, and the complexity of the construction process. The specific selection needs to be comprehensively considered based on project requirements such as insulation performance, construction difficulty, and cost.
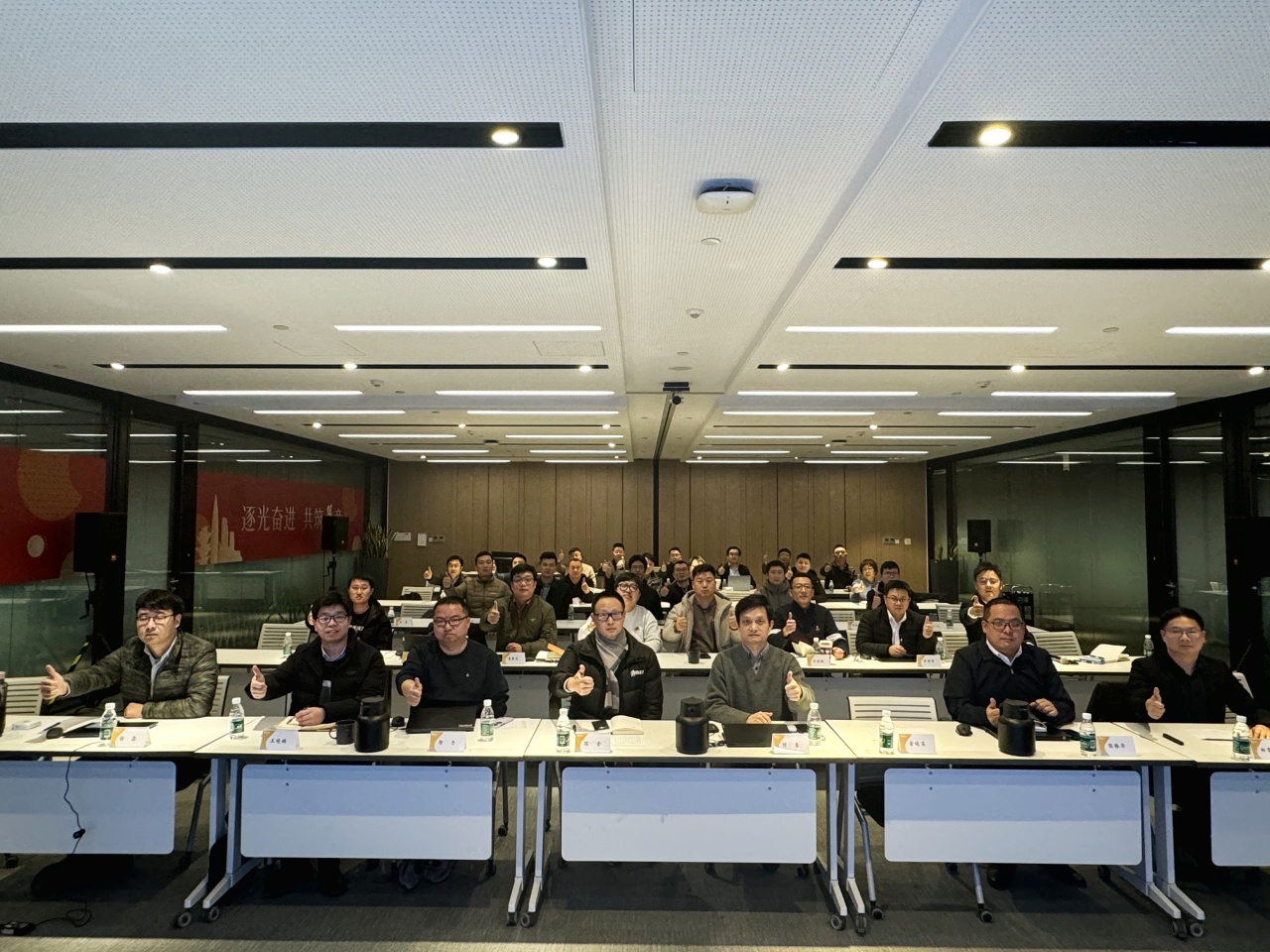

Winning the first prize in this competition not only recognizes FORCITIS' technological capabilities in the industry, but also affirms its contribution to the development of the industry.
In the future, FORCITIS will continue to be committed to technological innovation, engage in broader and more diverse exchanges and cooperation with industry colleagues, jointly promote the sustainable development of the construction industry, and help more projects achieve the goal of ultra-low energy consumption or even near zero energy consumption.