Stone is one of the earliest materials used in construction, which has relatively good durability. Many ancient buildings in the world use stone as the main building material, and stone is still widely used in today's building environment. Natural stone is characterized with uniform structure, hard texture, wear resistance, beautiful color, and appearance, which can be maintained for more than a hundred years. Because of its unique physical properties and its beautiful patterns, it has become a good material for construction. Many advantages of stone can not be replaced by other materials.
Stone supply industry is a large industrial chain: in the early stage, it includes stone resource excavation, geological exploration, mining, raw material transportation, stone trade, stone processing, product transportation, etc. In the later stage, it will involve mechanical processing, building decoration, decoration design, stone variety selection, physical and chemical index testing, construction and installation, etc;
Large stone suppliers are usually large professional stone companies integrating mining, processing, engineering and import and export trade. In order to ensure the smooth development of the follow-up work of the stone curtain wall project and ensure the high-quality and timely supply of curtain wall stones, it is an important task to select stone suppliers with mines, certain reserves of raw materials, strong processing capacity and good comprehensive strength for field investigation before ordering stone curtain walls.
To inspect the building stone board, we need to understand the process flow of stone processing first, and determine the important concerns of the inspection according to the process flow.
Stone production process:
Because of the variety of stone materials, the quality of stone materials is not entirely comparable, so it is suggested that architects and owners should first determine the variety of stone materials, and then select excellent stone enterprises for field investigation.
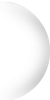
The inspection of stone processing plants mainly includes stone category and scale, stone processing equipment, and the investigation and understanding of the processing of finished stone products, especially special-shaped, ultra-thin and special processing technology.
Inspection process of processing plant
1) Inspect the overall scale. The size of the stone processing plant, whether the operation and performance are good, whether the quality assurance system is complete, and whether the block reserve is sufficient. These relationships are related to the supply capacity of stone manufacturers.
Figure 1: Processing Plant Area
Figure 2: Block Reserve
2) Inspect the processing equipment. See whether the type and quantity of processing equipment can meet the needs of batch supply, whether the equipment is in good condition, and whether the stone processing technology is reasonable.
Stone curtain walls are mostly complex in shape, and there are many special-shaped stones, such as complex jigsaw puzzles, hollow columns, conical columns, elliptical columns, column heads, column bases, twisted patterns, arc plates and other special-shaped plates, which need to be processed by CNC machine tools.
Stone processing mainly includes sawing and polishing, each with different processing machinery. Modern processing equipment is the best guarantee of product processing quality and processing accuracy.
Frame saw or gang saw (Figure 3, 4). Because of the use of steel grit, it is also called steel grit saw, which is a common mechanical equipment for the production of granite and marble slabs. Nowadays, the obvious development trend of steel abrasive saw is automation and large-scale. At present, the largest frame saw in the world can produce 120 plates at a time, and the saw blade stroke is 80 cm. In addition, the sawing process parameters can be automatically adjusted within a certain range, and the connecting rod stroke can be automatically compensated without stopping. The sawing process of sand saw is discontinuous, so the sawing speed can not be fast, generally not more than 2m/s, so one of the ways to improve productivity is to develop towards large-scale and increase the number of sawing per batch.
Figure 3: Steel Grit Saw
Figure 4: Steel Grit Saw
Figure 5: Diamond Seesaw
Figure 6: Special Cutting Saw
Figure 7: Gantry (Bridge) Diamond Machine
Under the control of the computer, the numerical control wire saw (Figure 8) can carry out visual processing according to the input size and data, and can process any two-dimensional curve, such as arc surface, paraboloid, etc.; the six-axis wire saw can realize six-axis linkage, and can process any space curve.
Figure 8: Data Rope Control
Figure 9: Water Jet Cutting Machine
According to the degree of processing automation, stone grinding and polishing machines can be divided into single-block grinding and polishing machine and continuous grinding and polishing machine (Fig. 10, 11).
Figure 10: Fully Automatic Grinding and Polishing Machine
Figure 11: Fully Automatic Grinding and Polishing Machine
Figure 12: Edging, Grooving and Chamfering
Figure 13: Edging, Grooving and Chamfering
Figure 14: Versatile Profile
The multifunctional special-shaped machine (Fig. 14) can be used to process fire surface, litchi surface, etc. It adopts full-automatic starting operation line, automatic ignition, automatic bridge pendulum and automatic plate feeding; the surface depth of the finished product is consistent, uniform, smooth and free of thorns, with good hand feeling and flatness controlled within 0.5mm, which is by no means comparable to manual processing.
Figure 15: Three-dimensional Glue Line
Figure 16: Infrared Bridging Machine
The infrared bridge cutting machine (Fig. 16) is mainly used for cutting standard specification boards. The automatic feed cutter is controlled by the program, which effectively solves the problem that the cutting size deviation increases due to the change of the wear thickness of the saw blade, and ensures that the cutting size deviation is less than 0.5 mm; the worktable can rotate 90 degrees, and the angle is automatically adjusted, which ensures that the cutting length and width of the specification plate are vertical, and the angle deviation is less than 0.5.3)
3) Inspect quality management. In terms of quality management, it depends on whether the supplier has special design lofting and review personnel, quality inspectors, factory inspection and qualified release system. For example, before leaving the factory, the quality inspector should check whether there are obvious cracks on the board surface (Fig. 17).
Figure 17: Inspection Panel
Pay attention to the production environment and management of the factory, enter the workshop to check the variety of granite, whether the articles are placed neatly and reasonably, and whether the operation process is standardized (Fig. 18 and 19).
Figure 18: Rough Board Placement
Figure 19: Finished product placement
Understand what means and methods the processing plant uses to control the quality of products. Stone is a natural product, so there are inevitably differences in color difference and pattern size. How to ensure that these products with color difference and pattern size difference have good effect and beautiful feeling after installation? This problem can be solved by tracing the number of the stone processing process. For example, the method of "layout without direct light" is used for color mixing of stone slabs (Fig. 20), so as to avoid the misjudgment of human eyes on color caused by inconsistent incident angles of light and different brightness of light, so as to achieve the most ideal effect of color difference control, and ensure that the stone achieves a large area of natural color transition and perfect decorative effect. After layout adjustment, each specification board is sequentially numbered, and the goods can be installed in sequence upon arrival at the construction site to ensure the overall decoration effect of the project.
Figure 20: Layout without Direct Light
Stone is a building material of processing size, so it is necessary to understand the specifications and sizes of stone blocks and the rate of production after processing in detail during the investigation, so as to make the best use of everything and reduce the loss rate.
Figure 20: Typesetting and drying
II. Inspection of quarry
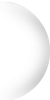
Inspecting the processing plant only understands the processing capacity and technical strength of the supplier. Whether the supplier can meet the supply of large-scale plates and guarantee the supply of follow-up stones depends on whether he has a mine and whether he operates legally.
Quarry inspection process
1) Check the business license. The quarry shall have complete business license, mining license and safety production license, and belong to legal mining; the operation and performance of the contract shall be good.
Figure 22: Quarry
2) Check the quality of ore body. The ore body has good glossiness, uniform particle size, clear pattern, no destructive lines and heterochromatic impurities, and the color of stone is basically the same without large color difference (Fig. 23 and 24).
Figure 23: Mining Face
Figure 24: Block
3) Physical properties of stone. Density, water absorption, bending strength, corrosion resistance, weathering resistance and radioactivity must meet the requirements of national standards.
4) Mine reserves. It can meet the requirements of quantities, and the mining method conforms to the provisions of safe mining; the block size is moderate, the shape is regular, and it can be supplied in place at one time (Figure 25, 26).
Figure 25: Block Yard
Figure 26: Reserve to be Transported
5) Transportation capacity. There is enough transportation capacity to transport the blocks out of the mountain (Fig. 27). The blocks in the quarry are generally transported out of the mountain by trucks. The traffic conditions in the mountain area are general, and they are usually greatly affected by bad weather.
Figure 27: Truck Transport
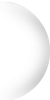
Focus on the investigation of stone processing plant
1) Processing equipment. Advanced process equipment, strong production and processing capacity and whether these equipment are well developed and utilized are the key control points to effectively ensure the construction period and quality of the project.
2) Quality management. Strict and perfect quality management system is another key control point to ensure product quality.
3) Stone raw materials. Do you have a good research, understanding and grasp of all kinds of stone raw materials of the processed products.
Focus of quarry investigation
1) Reserves of the quarry. Whether the reserves of stone blocks in the quarry can ensure timely supply according to the requirements of the construction period and meet the needs of the project progress.
2) Operation period of quarry. First, whether the total mining volume of the mine can meet the needs of the project; second, whether there is the possibility of restricting or terminating mining for the reasons of environmental and resource protection.
3) Traffic conditions. Whether the traffic is convenient and smooth, and whether there is the possibility of supply termination and delay due to climate reasons.
Safety first
Most of the quarries have high mountains and steep slopes, and the roads are winding up, so the road conditions are poor. The deep open quarries with vertical mining are all caverns with a depth of nearly 100 meters, so attention should be paid to safety when investigating and watching.